Materials for Robot Manufacturing and Frame Structures: Comprehensive Predictions and Analysis
Executive Summary
Robot manufacturing materials are undergoing a fundamental transformation driven by advances in material science, cost reduction pressures, and evolving performance requirements. Traditional materials (aluminum and steel) will remain dominant through 2030 but face increasing competition from advanced composites, smart materials, and bio-inspired solutions that offer superior performance characteristics for next-generation robotics applications.
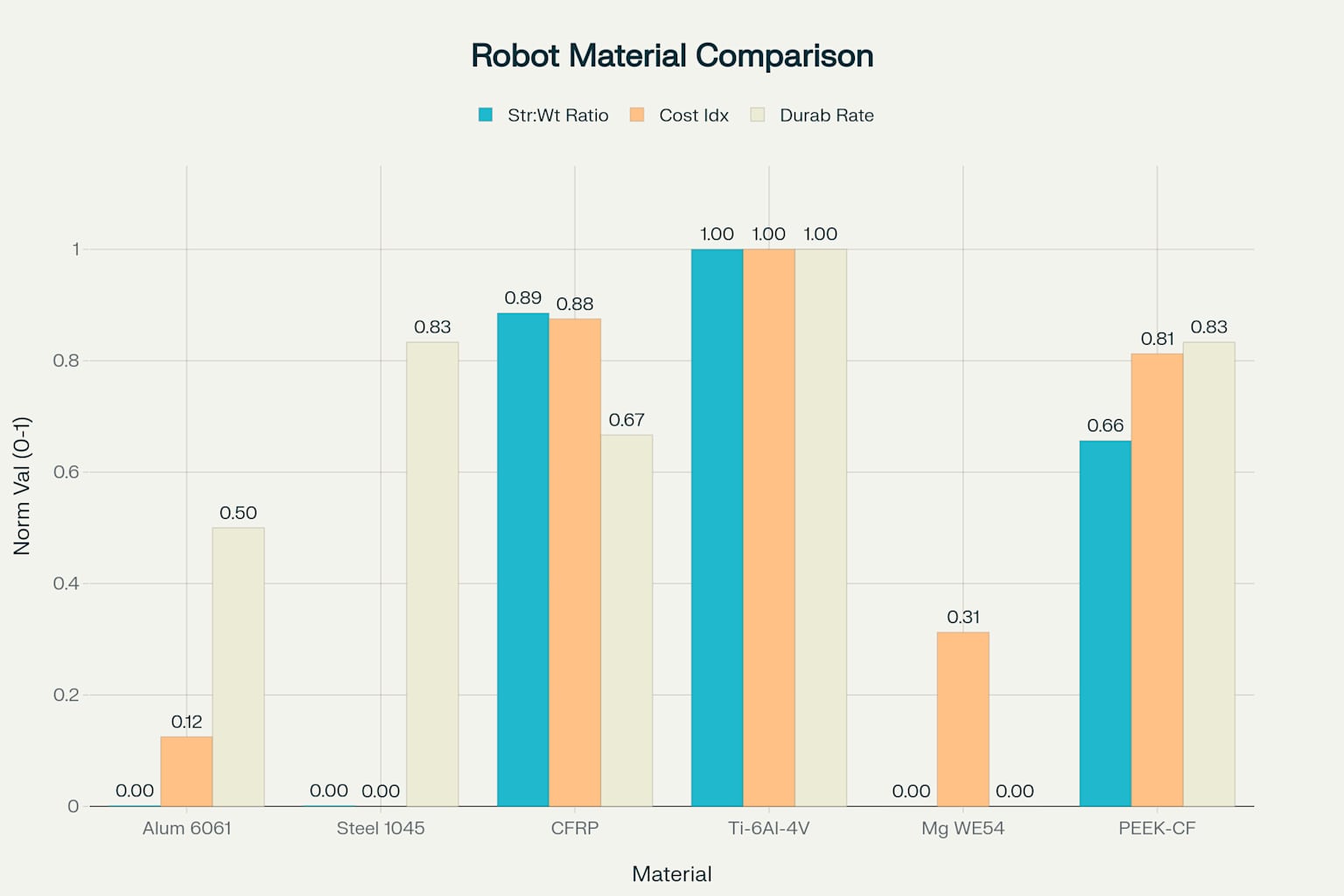
Robot Materials Comparison: Key Performance Metrics for Manufacturing Selection
Current Material Landscape (2025)
Traditional Materials – The Foundation
Aluminum Alloys (6061-T6) continue to dominate robot frame manufacturing, representing approximately 70% of current usage. The material offers an optimal balance of properties:
- Strength-to-weight ratio: 25.5 (comparable to steel but 65% lighter)
- Density: 2.73 g/cm³ (one-third of steel)
- Cost: Approximately $2-4 per kg (highly economical)
- Machinability: Excellent with standard CNC equipment
- Corrosion resistance: Superior to steel without coating
Steel (including stainless grades) maintains its position for high-load applications requiring exceptional strength and durability. Despite being 3x heavier than aluminum, steel offers:
- Tensile strength: 355-800 MPa depending on grade
- Cost effectiveness: $1-2 per kg for standard grades
- Proven reliability: Decades of industrial robot applications
- Temperature resistance: Superior high-temperature performance
Advanced Composite Materials – Rising Stars
Carbon Fiber Reinforced Plastics (CFRP) are experiencing exponential growth in robotics applications. Key advantages include:
- Strength-to-weight ratio: Up to 180 (5x better than aluminum)
- Tensile strength: 3,500+ MPa in fiber direction
- Density: 1.6-1.8 g/cm³ (40% lighter than aluminum)
- Applications: Industrial robot arms, aerospace robotics, precision mechanisms
Research demonstrates CFRP can reduce robot arm weight by 42.3% compared to aluminum frames while maintaining equivalent strength. The F44 packaging robot successfully replaced aluminum arms with CFRP, achieving dramatic improvements in dynamics and reduced inertia.
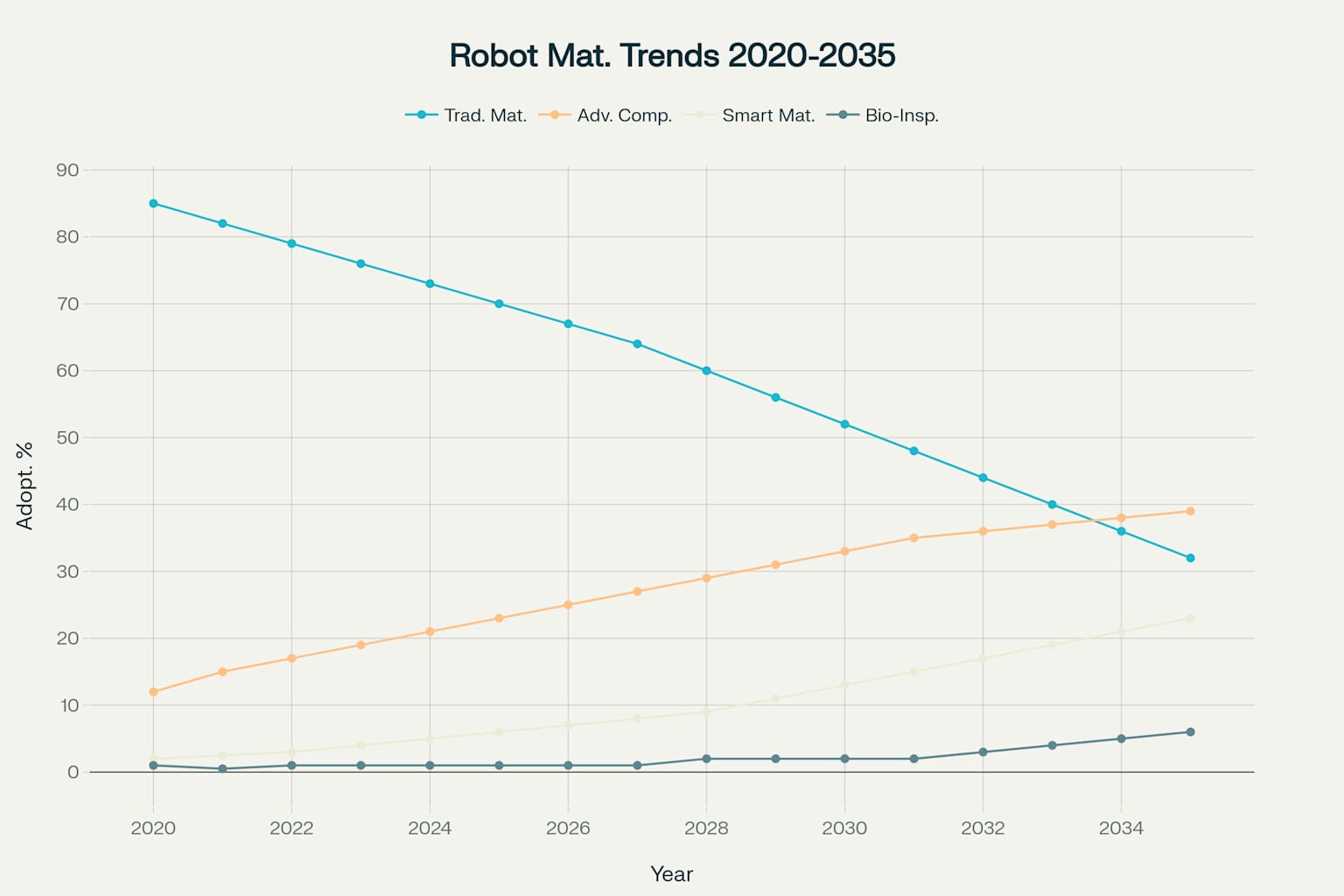
Evolution of Robot Material Usage: Historical Trends and Future Predictions (2020-2035)
Material Selection Trends and Predictions (2025-2035)
Market Evolution Patterns
Based on comprehensive industry analysis, robot material usage will undergo significant shifts over the next decade:
2025-2030 Transition Period:
- Traditional materials will decline from 70% to 52% market share
- Advanced composites will grow from 23% to 33%
- Smart materials will expand from 6% to 13%
- Bio-inspired materials will emerge from 1% to 2%
2030-2035 Acceleration Phase:
- Advanced composites will become the dominant category at 39% market share
- Smart materials will capture 23% of applications
- Traditional materials will stabilize at 32% for cost-sensitive applications
- Bio-inspired materials will reach 6% in specialized applications
Emerging Material Technologies
Titanium Alloys – The Premium Solution
Titanium Ti-6Al-4V is experiencing unprecedented growth in humanoid robotics, with 217% year-over-year order surge in Q1 2025. Key drivers include:
- Strength-to-weight ratio: 200+ (8x better than steel by weight)
- Biocompatibility: Critical for medical and service robots
- Fatigue resistance: 3x better than stainless steel
- 3D printing optimization: AI-driven processing reducing costs by 50%
Major applications include humanoid robot joints (Tesla Optimus Gen3, Boston Dynamics Atlas V11) and bionic joint systems where precision and durability are paramount.
Magnesium Alloys – Ultra-Lightweight Champions
Magnesium alloys offer the lowest density (1.74 g/cm³) among structural metals while maintaining excellent strength characteristics. Research indicates:
- Weight reduction: Up to 26% speed increase in packaging robots
- Strength-to-weight ratio: 25.3 (comparable to aluminum and steel)
- Damping capacity: Superior vibration absorption
- Environmental benefits: Fully recyclable and biodegradable
Surface treatment technologies are advancing to address corrosion resistance challenges, enabling broader industrial adoption.
Smart Materials Revolution
Shape Memory Alloys (SMAs)
SMAs, particularly Nickel-Titanium (NiTiNOL), are transforming robot actuator design. These materials offer:
- High energy density: Superior to conventional actuators
- Bio-compatibility: Ideal for medical robotics
- Self-actuation: Temperature-responsive movement without external motors
- Precise control: Nanometer-level positioning accuracy
Applications range from robotic hands and crawlers to aerospace deployment mechanisms and wearable exoskeletons.
Self-Healing Materials
Revolutionary biosynthetic polymers are enabling robots to repair themselves autonomously. Key breakthroughs include:
- Healing speed: Reduced from 24 hours to 1 second with localized heating
- Strength recovery: 2-23 MPa strength after healing
- Electrical continuity: Liquid metal droplets maintain power/data transmission during damage
- Applications: Soft robotics, hazardous environment operations, space exploration
Penn State researchers developed squid-inspired proteins that create self-healing actuators for pneumatic robots, addressing the critical reliability challenges in soft robotics.
Advanced Skin Materials
Artificial skin technologies are enabling new robot capabilities through multifunctional materials:
- ElectroSkin: Combines actuation and sensing in single material structure
- Nanocellulose composites: Self-healing electronic skin with 409% strength increase
- 2D-material hydrogels: Protection against heat, chemicals, and electromagnetic radiation
- TPU-based pressure sensors: Low-cost, 3D-printable tactile sensing
Manufacturing Cost Analysis and Predictions
Current Cost Structure
Robot manufacturing costs are declining rapidly due to technological advances and economies of scale:
- Industrial robot costs: Expected to drop 50-65% by 2030
- Material cost impact: Represents 15-25% of total robot cost
- 3D printing benefits: Up to 75% material waste reduction
- Learning curve effects: 50% cost reduction for every doubling of production
Material Cost Projections (2025-2035)
Premium Materials Becoming Accessible:
- Titanium: AI-optimized processing reducing costs by 40-50%
- Carbon fiber: Mass production scaling reducing costs by 30-40%
- Smart materials: Volume manufacturing enabling 60-70% cost reductions
Cost-Performance Optimization:
- Aluminum: Remains most cost-effective for general applications
- Magnesium: Emerging as cost-competitive for lightweight requirements
- Hybrid solutions: Combining materials for optimized cost-performance ratios
Application-Specific Material Selection
Industrial Robots
Heavy-duty applications: Steel frames with aluminum components for optimal cost-strength balance
Precision manufacturing: Carbon fiber structures for reduced vibration and increased accuracy
High-speed operations: Magnesium alloy components for maximum speed and efficiency
Service and Humanoid Robots
Humanoid joints: Titanium alloys with 3D-printed structures for bio-compatibility and precision
Soft robotics: Self-healing polymers and shape memory alloys for adaptive behavior
Medical applications: PEEK-carbon fiber composites for biocompatibility and sterilization resistance
Specialized Applications
Aerospace robotics: Carbon fiber and titanium for extreme environment resistance
Underwater robots: Corrosion-resistant composites and protective skin materials
Extreme environments: 2D-material integrated skins for thermal and chemical protection
Future Predictions and Recommendations
Technology Roadmap (2025-2035)
2025-2027: Composite materials mainstream adoption in high-performance applications
2027-2030: Smart materials integration for adaptive and self-healing capabilities
2030-2035: Bio-inspired materials enabling new robot architectures and functionalities
Strategic Recommendations
For Robot Manufacturers:
- Invest in composite manufacturing capabilities for competitive advantage
- Develop smart material integration expertise for next-generation products
- Establish titanium alloy supply chains for premium market segments
- Partner with material science institutions for cutting-edge material access
For Component Suppliers:
- Focus on cost-effective aluminum processing for volume markets
- Develop specialized coatings and treatments for material enhancement
- Invest in 3D printing technologies for complex geometry manufacturing
- Build expertise in hybrid material systems for optimized solutions
Conclusion
The robot materials landscape is undergoing unprecedented transformation, driven by advances in material science, manufacturing technologies, and evolving performance requirements. While traditional materials will remain important for cost-sensitive applications, advanced composites, smart materials, and bio-inspired solutions will capture increasing market share through superior performance characteristics.
Key success factors for the next decade include:
- Material technology investment and integration capabilities
- Cost optimization through advanced manufacturing processes
- Application-specific material selection for optimal performance
- Supply chain development for emerging material technologies
Organizations that strategically invest in advanced materials and develop integration expertise will gain significant competitive advantages in the rapidly evolving robotics market. The transition from traditional to smart materials represents not just an evolution in manufacturing, but a fundamental shift toward more capable, adaptive, and intelligent robotic systems.